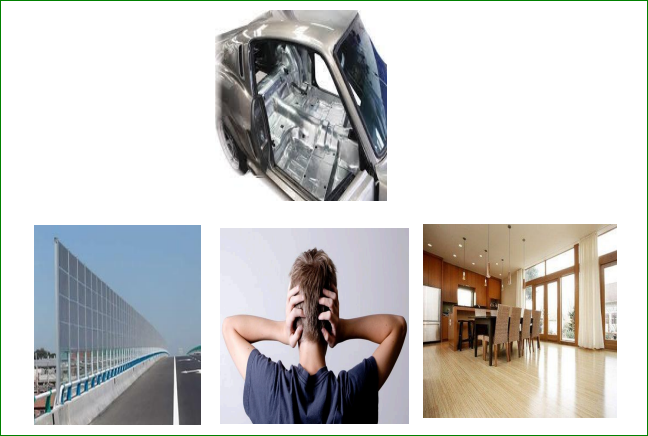
By Zarna Sanghavi
ABSTRACT
Noise pollution has become a significant environmental issue and poses a growing threat to public health. The harmful effects of noise include hearing impairment, sleep disturbances, fatigue, cardiovascular and psychophysiological issues, decreased performance, increased annoyance, and negative social behaviours. Thus, managing and reducing noise from sources such as traffic, industrial settings, workplaces, and homes is crucial. Unwanted and potentially harmful noise is a byproduct of various modern engineering activities and other operations. Noise within enclosed spaces can be particularly problematic, but several practical solutions are available. One effective approach is using textiles for noise reduction, which offers two main benefits: low production costs and lightweight properties.
Keywords:- acoustic, soundproofing textiles, technical textiles
OBJECTIVES
- To understand the different textile materials used in acoustic performance technology.
- To know the recent advancement in technology of soundproofing textiles.
- To know the different places where sound-resisting textiles are used.
INTRODUCTION
Sound is an important part of our life on the other hand if it is out of control it will create problems so we need sound but in control. The use of textiles for noise reduction is based on two major advantages of this material: low production costs and small specific gravity. Textiles play a dual role in aesthetic as well as functional. So it is an added advantage to use as acoustic. Out of textiles nonwoven are preferred to use as acoustic due to their more porous structure, surface area and low cost of production. Renewable material is based on two alternatives for the production of ecologically friendly products and low production costs.
Acoustics: It is defined as the scientific study of sou
nd which includes the effect of reflection, refraction, diffraction and interference.
Sound: It is an alternation of pressure that propagates through an elastic medium such as air which produces an auditory.
Noise: It is an unwanted sound.
Soundproofing is any means of reducing the sound pressure concerning a specified sound source and receptor. These are several basic approaches to reducing sound, increasing the distance between source and receiver using noise barriers to reflect or absorb the energy of the sound waves.
Review of Literature
The primary material used for sound absorption is paper pulp, which is suitable for use in places such as conference halls, auditoriums, theatres, classrooms, hospitals, offices, airplanes, and automobiles. Key factors influencing sound absorption include the type, dimensions, thickness, density, resistance, and porosity of the fibres. Additionally, recycled rice straw waste particles are also employed due to their excellent acoustic properties. The primary properties affecting sound absorption are density, thickness, and porosity. To create a pulp composite, recycled paper is chopped and ground with an appropriate amount of water. Excess water is drained using a nylon woven fabric, and then sisal fibres are cut to the required length. A homogeneous mixture is formed and placed into moulds to create the desired blocks. After 24 hours, the blocks are removed and left to dry at room temperature for one week. The result shows that increasing the sisal fibre content enhances porosity. There are three stages in developing the mechanical properties, involving combining chemical and physical interactions. The first stage is chemical, where paper pulp and sisal fibres undergo a hydration reaction. In the second stage, which is physical, the paper pulp begins to crystallise, forming a matrix around the fibres. The final stage can continue for many years. The sound-absorbing capacity of Sisal Fiber Reinforced Recycled Paper Composites (SFRRPC) blocks is related to their density. Increasing the sisal fibre content in the composite boosts porosity. For a high sound absorption coefficient, density should increase along with the propagation of sound waves, with pores being a crucial factor. The SFRRPC blocks have superior acoustic properties compared to plywood and are lightweight and low-cost. Therefore, SFRRPC blocks could be used as construction materials for sound control in buildings (E Tholkappivan, D Saravana, et.al.,2015)
In today’s world noise has become a major environmental issue and has a bad impact on human well-being. The higher quality sound absorption materials are used which are light, thin, cheap, safe and eco-friendly. The raw material undergoes oxidation, carbonization and activation and forms Activated Carbon Fibre (ACF). When preparing for the raw material two basic steps involve carbonization and activation. Carbonization is achieved when oxidised fibre under the protection of inert gas experiences a change in temperature from an initial degree to a higher degree and can remove the non-carbon elements easily. Activation is achieved when carbonised fibre reacts with the oxidising gas at high temperature and activated carbon fibre is produced. Activated carbon fibre felt has a unique feature. It has a three-dimensional structure. It is an ideal porous material for sound absorption. The most common sound absorption fibres include natural fibres, inorganic fibres, synthetic fibres and fibre composite. Natural fibre has better performance, and high frequencies and can be disposed of and eco-friendly and safe. The research has been done on cotton, hemp, coconut, wool and tea fibre which are natural fibres. Inorganic fibre like glass fibre is the most typical material. When it is prepared nonwoven composites are layered with cotton, surface with glass fibre, cotton fibre and activated carbon fibre. The composites with activated carbon fibre have better performance so activated carbon fibre is used as sound absorption material. The density and thickness should be kept within a certain range for the absorption of sound. The effect of thickness, bulk density and fineness affect the sound absorption properties of activated carbon fibre felts (Yue Shen and Gaoming Jiang, 2014).
A peaceful and stress-free environment is a basic requirement for human comfort. Due to the rapid growth of modern industries, the environment in which we live gets disturbed. Noise pollution produced by these modern industries has been an increasing cause of concern and the development of soundproofing materials has become particularly important.
The textile material is made up of fibres of circular cross-section. For the absorption of sound waves irregular holes are created in fabrics. Shear Thickening Fluids (STFs) are slightly sticky liquids which have the property of solidifying under external impacts. STF’s fabric is made up of polyester yarn with 2,3,4,5 or 6 strands made into weft knitted fabric. A high-viscosity STF cannot easily penetrate the fabrics at room temperature so the fabric
In today’s world noise has become a major environmental issue and has a bad impact on human well-being. The higher quality sound absorption materials are used which are light, thin, cheap, safe and eco-friendly. The raw material undergoes oxidation, carbonization and activation and forms Activated Carbon Fibre (ACF). When preparing for the raw material two basic steps involve carbonization and activation. Carbonization is achieved when oxidised fibre under the protection of inert gas experiences a change in temperature from an initial degree to a higher degree and can remove the non-carbon elements easily. Activation is achieved when carbonised fibre reacts with the oxidising gas at high temperature and activated carbon fibre is produced. Activated carbon fibre felt has a unique feature. It has a three-dimensional structure. It is an ideal porous material for sound absorption. The most common sound absorption fibres include natural fibres, inorganic fibres, synthetic fibres and fibre composite. Natural fibre has better performance, and high frequencies and can be disposed of and eco-friendly and safe. The research has been done on cotton, hemp, coconut, wool and tea fibre which are natural fibres. Inorganic fibre like glass fibre is the most typical material. When it is prepared nonwoven composites are layered with cotton, surface with glass fibre, cotton fibre and activated carbon fibre. The composites with activated carbon fibre have better performance so activated carbon fibre is used as sound absorption material. The density and thickness should be kept within a certain range for the absorption of sound. The effect of thickness, bulk density and fineness affect the sound absorption properties of activated carbon fibre felts (Yue Shen and Gaoming Jiang, 2014).
A peaceful and stress-free environment is a basic requirement for human comfort. Due to the rapid growth of modern industries, the environment in which we live gets disturbed. Noise pollution produced by these modern industries has been an increasing cause of concern and the development of soundproofing materials has become particularly important.
The textile material is made up of fibres of circular cross-section. For the absorption of sound waves irregular holes are created in fabrics. Shear Thickening Fluids (STFs) are slightly sticky liquids which have the property of solidifying under external impacts. STF’s fabric is made up of polyester yarn with 2,3,4,5 or 6 strands made into weft knitted fabric. A high-viscosity STF cannot easily penetrate the fabrics at room temperature so the fabric is treated with ethanol. The fabric is soaked in the solution for about 30 minutes. Then it is dried in the oven at 80C for 30 mins. The STF treatment did not affect the flexibility of the fabric.
A single layer of fabric is very thin and has high porosity and it allows low-frequency sound waves to penetrate and pass through fabric. The increase in fabric surface density shows an increase in sound reduction. The propagation time of the sound wave in the fabric is prolonged and more sound energy is thus absorbed. When the sound energy is absorbed by the STF the sound waves penetrate the fabric. The sound insulation level of the STF-treated fabric very clearly increased with increasing surface density. The sound insulation performance of STF-treated fabrics was superior to untreated fabrics (Shan Li, Yan Wang, et.al., 2014)
Woven fabrics are generally the least effective as far as sound absorption properties are concerned. The greatest impact on the acoustic performance of textile material is flow resistance, porosity, air permeability and tortuosity (i.e. the structure factor). The sound absorbency of the fabric increases with airflow and fabric thickness. Fabric porosity is inversely proportional to the airflow resistivity. Hence the variation in fabric sound absorption property is inversely proportional to the fabric porosity. Fabric thickness inversely influences sound reduction by the fabric, particularly at high frequencies. Air permeability of multi-layer fabric not only decreases. The sound absorption coefficient gets higher at a certain air permeability and begins to reduce. The fabric also affects weave type, yarn, linear density, twist and fabric thickness which affect the sound absorption properties. Polyester fibres are used to produce spun yarns on a Howa Ring spinning frame under certain conditions. The sound absorption coefficient and air permeability of plain woven fabrics were tested using an air permeability tester and the thickness of the fabric was also measured with the standard compression tester.
Pick density is defined as the parameter denoting the number of filling yarns per unit length along the fabric length. Woven fabrics are a more effective means of sound absorption. To make the fabric the effect of fabric pick density, fabric thickness created by layering technique and weft yarn twist was given. The weft yarn linear density, fabric woven with pick density absorbs more sound than other fabrics. The six-layer sample woven at pick density has a higher NRC than a similar fabric woven at other pick densities. The rate of increase in NRC of layered fabrics is higher for woven at low pick densities. It also stated that the weft yarn twist is increased, fabric absorption coefficient is decreased. The higher rate of NRC increases in fabric woven at lower yarn twist is confirmed by the lower air permeability of those fabrics (Parham Soltani and Mohammad Zarrebini, 2013)
Noise is greatly affecting the day to day activities and can cause various health problems. Since fibrous material has tremendous potential for acoustic insulation. Factors such as fibre size, resistance to the passage of airflow, porosity thickness and density have been seen. Nonwoven shows greater noise reduction than woven. The nonwoven fabrics are produced from mineral wool and recycled fibre, which is a mixture of polypropylene, acrylic, cotton, polyester and other fibres. The mass per unit area, thickness and density of the samples are different. One sample was laminated with an aluminium foil and another one was produced from mineral wool that is mostly currently used in the construction site.
The nonwoven made from mineral wool is better at reducing sound. It is also seen that the nonwoven laminated with aluminium foil has a similar behaviour to the mineral wool nonwoven. In high frequencies both nonwovens’ performance is similar but in the region of human ear perception, the nonwoven with aluminium foil exhibits more sound reduction efficiency. The acoustic insulation behaviour of nonwoven fabrics strongly depends on their composition and structure.
An improvement in sound insulation can be observed with the increase in nonwoven thickness. Lamination of a second material such as aluminium foil improves the acoustic insulation performance of the thermo-bonded nonwoven fabric. Therefore the thermo-bonded nonwoven fabric with aluminium foil lamination was found to provide the best sound insulation performance than the other nonwoven samples. It also shows better sound reduction efficiency as compared to the nonwovens made from mineral wool in the frequency range of human ear perception (R. Carvalho, S. Rana, R. Fangueiro and F.Soutinho, 2013).
CONCLUSION
There is already a high penetration of nonwovens in construction sectors. When they have to choose a variety of products, manufacturers consider the following criteria: economics, durability, aesthetics, processability, moldability, and added benefits which are the main driving forces of nonwoven in the construction industry worldwide. The use of textiles for noise reduction is based on two major advantages of these materials, namely low production costs and small specific gravity.
As the acoustic textile materials currently used in motor vehicles. The main challenge for acoustic automotive textiles manufacturers can be synthesised as follows: process recyclable materials today, optimally recycle them tomorrow and optimally dispose of them the day after tomorrow.
REFERENCES
BIBLIOGRAPHY
M. D. Teli, A Pal & Dipankar Roy, Vol. 32, June 2007, Efficiency of nonwoven materials as sound insulator, Indian Journal of Fiber & Textile Research
Y. Chen and N. Jian, Vol. 79(3), 2009, Carbonized and Activated Non- woven as High Performance Acoustic Materials: Part II Noise Insulation, Textile Research Journal
N. Jing, J. Y. Chen, D. Y. Parikh, 6th August 2009, Acoustical evaluation of carbonized and activated cotton nonwovens, Bioresource Technology
Yanping Liu, Hong Hu, Vol. 80, 2010, Sound Absorption Behavior of Knitted Spacer Fabrics, Textile Research Journal
F. Chevillotte, 2011, Controlling Sound absorption by an upstream resistive layer, Applied Acoustics
Parham Soltani and Mohammad Zerrebini, Vol. 82(9), 2012, The analysis of acoustical characteristics and sound absorption coefficient of woven fabrics, Textile Research Journal
R. Carvalho, S. Rana, R. Fangueiro and F.Soutinho, June 13th to 15th 2012, Noise Reduction Performance of Thermo- bonded Nonwovens, 12th World Textile Conference AUTEX
Parham Soltani and Mohammad Zarrebini, Vol. 9, 2013, Acoustic performance of woven fabrics in relation to structural parameters and air permeability, Journal of The Textile Institute
Shan Li, Yan Wang, Juan Ding, Huimin Wu and Yaqin Fu, Vol.84(9), 2014, Effect of shear thickening fluid on the sound insulation properties of textiles, Textile Research Journal
Yue Shen and Gaoming Jiang, Vol. 105, 2014, Effect of different parameters on acoustic properties of activated carbon fiber felts, The Journal of the Textile Institute
E Tholkappivan, D Saravana, R Jagasthitha, T Angeswari & V T Surya, Vol.40, March 2015, Modelling of sound absorption of sisal reinforced paper pulp composites using regression model, Indian Journal of Fiber and Textile Research