By Rashmi Agrawal
B.Des (Fashion Design)
Amity School of Fashion Technology, Amity University Mumbai
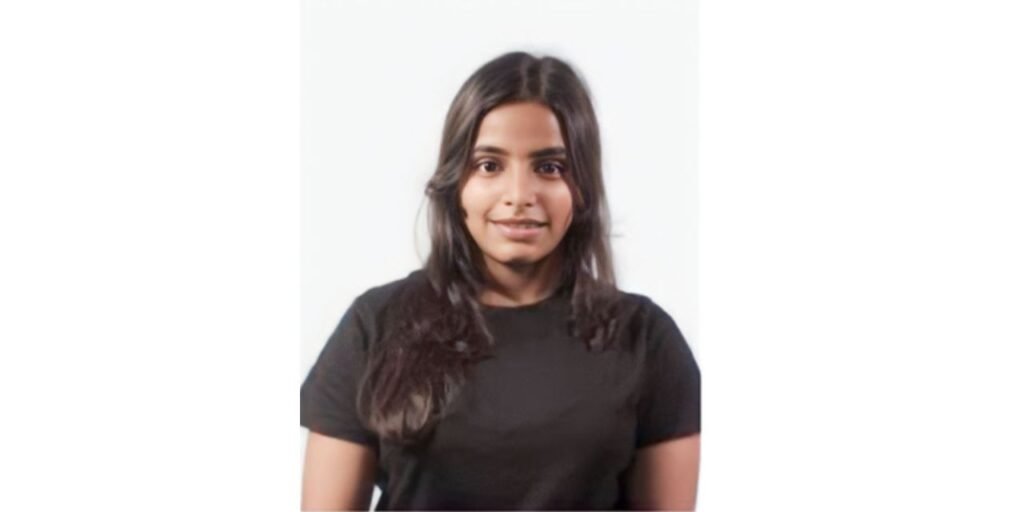
Rashmi Agrawal
Nonwoven technologies enable the production of a vast array of products for an increasing number of end applications. Evidence points to felting as the first technique for turning fibers into fabric. Felting harnesses the scaly structure of wool to firmly bind the fibers together. While certain manufacturing techniques used in the nonwoven business today are a result of modern engineering created to work with man-made materials, others are derived from this ancient way of fabric formation. Although the exact beginnings of the contemporary nonwovens business are unknown, The Nonwovens Institute in Raleigh, North Carolina, claims that the word “nonwoven fabrics” was initially used in 1942, during a time when fabrics were produced by adhering fibre webs together with adhesives.
In the decades since the word was originally used, an astounding diversity of technologies have arisen for producing items for filtration, automotive, medicinal, hygiene, geotextile, agro textile, floorcovering, and even garment purposes. This article describes some of the most recent technical developments that makers of nonwoven fabrics and products might benefit from.
Nonwovens are not usually the greatest candidates for manufacture using standard cut-and-sew methods because of their non-conventional nature. Since the pandemic started and personal protective equipment (PPE) became necessary, there has been an increased focus on ultrasonic technologies, which employ high-frequency sound waves to heat and plasticize man-made fiber nonwoven materials. Sonobond Ultrasonics, located in West Chester, Pennsylvania, claims that ultrasonic bonding techniques can quickly produce robust, sealed edges and secure barrier seams that satisfy regulatory standards. These better bonding at pressure sites enable final products free from fraying, unwinding, glue gaps, and stitch holes. It doesn’t need a thread, and production increases with quicker manufacture.
Sonobond offers equipment for bonding, seaming, slitting, cutting, and trimming. Often, a single machine may handle several operations in a single phase. Among Sonobond’s products, SeamMaster® Ultrasonic Sewing Machines are the most popular. SeamMaster’s innovative continuous rotational action produces soft, smooth, robust, and sealed seams. According to the business, the machine’s ability to do many tasks at once opens up a wide range of assembly applications. For example, with the right equipment, the SeamMaster can swiftly glue, seam, and trim all in one step. Sonobond claims that the pace may be up to 10 times faster than glue machines and up to four times faster than a traditional sewing machine. Since the SeamMaster’s design is akin to that of a traditional sewing machine, minimal operator training is necessary.
Sonobond’s technology is used in lint-free wound dressings, face masks, surgical gowns, pillows, mattress covers, and disposable shoes in the medical nonwovens industry. A wide range of filtration products, including heavy-duty filter bags, spill clean-up cloths, oil containment booms, pleated HVAC and HEPA filters, and liquid, gas, and air filters, may be made using Sonobond’s ultrasonic technology. To help choose the best method for the job, Sonobond offers a free Ultrasonic Bonding Viability Test using the nonwoven materials provided by the customer. After that, the customer may see the results and understand what the provided solutions are capable of.
Herrmann Ultrasonics Inc. of Bartlett, Illinois offers a unique ultrasonic method for anchoring elastic threads in diapers. The business creates a tunnel between two nonwoven layers and feeds the stretched elastic through it using a creative method. Following the fabric’s welding at predetermined bonding locations, it is cut and relaxed. The new anchoring process may operate intermittently or continuously. The technology, according to the corporation, minimises production costs, increases the process window, decreases breakage risk, and simplifies elastic handling. According to Herrmann, a variety of material combinations, elastic and elongation sizes, and speed variations have all been successfully tested.
Based in Germany, an established designer and producer of sleeves and embossing rollers for decorating spun bond and thermally bonded nonwovens, Saueressig Surfaces is a Matthews International Corp. subsidiary. The company uses both the newest laser engraving techniques and complex molettage procedures. The customisation possibilities are increased by hardened rollers, microporous shells, and basic, and structure dams. New 3D embossing and apperturing solutions have been developed recently. These can be used offline, with high-precision hot rollers that have intricate and precise engraving patterns, or inline, with nickel sleeves, during the hydroentangling process. These advancements allow for the creation of designs with three-dimensional effects that are flexible, have improved tensile strength, and have good air/liquid permeability. Saueressig may also produce 3D prototypes while taking base material, engraving pattern, foundation weight, and color into consideration in order to assist clients in coming up with the finest options for their finished items. The US representative for Saueressig Surfaces is called Fi-Tech.
Graf + Cie., a Swiss-based manufacturer of clothing for flat and roller cards, is a member of Rieter’s Components Business Group. Graf provides the nonwoven industry with their Hipro Metallic Card Clothing. According to Graf, the use of creative geometry in the design may boost output in nonwoven applications by as much as 10% when compared to conventional clothing. Graf claims that the Hipro teeth’s specifically designed front hump enhances fiber retention. Production can be increased by up to 10% with an efficient web transfer from the cylinder to the doffer. A precise fibre transfer to and from the cylinder also reduces the number of web failures.
The clothes can be customised to the application and the fibres to be processed because they come in a range of steel alloys and surface finishes, making them appropriate for both high-performance and ordinary cards. Hipro Card Clothings are suitable for various rollers, such as workers, doffers, and condenser rollers, and are made for all forms of man-made fibre produced in the nonwoven sector. Graf writes. Applications in the automotive, filtration, floor covering, medical, and hygiene sectors are perfect for Hipro.
Reifenhäuser Reicofil GmbH & Co. KG, a German company subsidiary of Reifenhäuser GmbH & Co. KG that specializes in spun-bond, melt-blown, and composite lines, offers sustainable nonwoven manufacturing options. According to the business, its Reicofil lines can process up to 90% of the polyethene terephthalate (PET) found in post-consumer waste for use in industrial applications. The company also provides technology for making sustainable materials, like bio-based raw materials, to make hygiene goods like diapers.
Additionally, Reifenhäuser Reicofil provides options for medical protective equipment, such face masks. To achieve N99/FFP3 standards, the firm ensures that highly dependable technology is used to produce nonwovens with a filtering efficiency of up to 99 per cent. The company understands the necessity of 100% reliable fabrics for such applications. For its new Health & Safety business segment, West Bridgewater, Massachusetts-based Shawmut Corp. recently purchased approximately 60 tons of specialised, high-precision melt-blown machinery from Reifenhauser Reicofil (see “Shawmut: Investing In The Future Of Advanced Materials,” TW, this issue).
Reifenhäuser Enka Tecnica, located in Germany, is an expert in creating replacement smart spinning beams, cassettes, and spinnerets that are tailored to fit any type of spunbond or meltblown line that is now in use. A company’s strengths allow it to improve existing lines and branch out into new markets including filtration, hygiene, and medicine. According to Enka Tecnica, the superior quality of the nozzle tips and capillaries ensures accuracy and consistency in the final output. Reduced preheating periods and enhanced heat output are achieved through the optimised sustainable energy concept incorporated into its melt-blown spinning beams. The success and happiness of our clients are our top priorities, according to Reifenhäuser Enka
Wilfried Schiffer, managing director of Tecnica. As a result, we place just as much importance on getting to know each of our clients personally as we do on delivering our incredibly high-quality products on schedule. A long-term, trustworthy cooperation is more important to us than turning a quick profit.
“We regularly set benchmarks for productivity and end-product quality in applications in the hygiene, medical, and industrial sectors,” says Markus Müller, sales director at Reifenhäuser Reicofil. Additionally, we offer our clients the option to use recycled or biobased raw materials to produce sustainable nonwovens. We help our clients take advantage of the opportunities presented by the worldwide transition to sustainability, or as we like to put it, “Next Level Nonwovens.”
REFERENCES:
https://www.textileworld.com/textile-world/features/2021/07/innovations-for-nonwovens-production/ https://www.nonwovens-industry.com/contents/view_breaking-news/2021-10-08/berry-introduced-3d-embossed-nonwoven/ https://reifenhauser.com/en/company/media/news-and-stories/press-releases/customers-in-Germany https://sonobondultrasonics.com/products/seammaster/