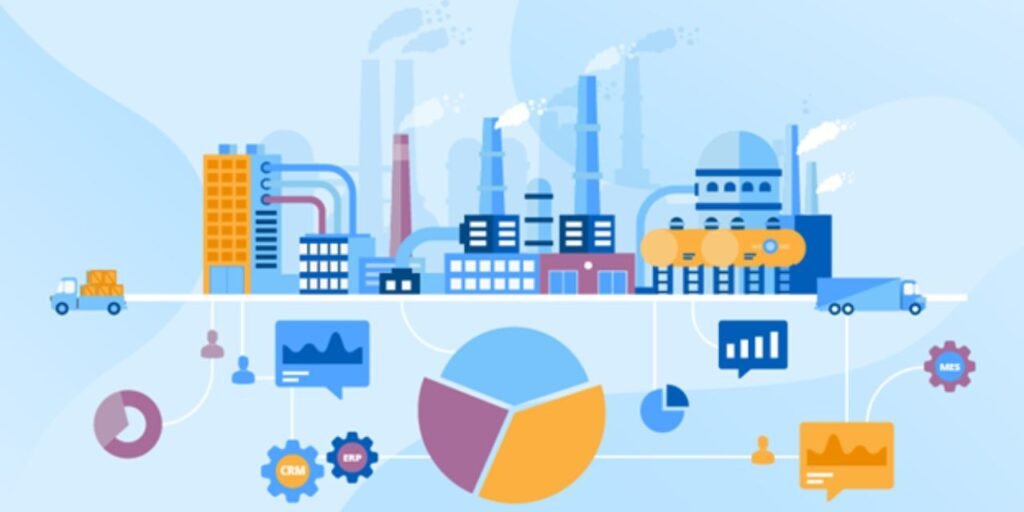
In the current business environment, manufacturing analytics has quickly become a vital tool that helps organizations to use data-driven insights to improve product quality, save costs, and optimize production processes. The need for efficiency, speed, and precision in the modern world has made conventional production techniques obsolete. Manufacturers may delve deeply into their operations with the help of analytics, revealing patterns and trends that would otherwise go unnoticed. Through the use of these data, businesses may make well-informed decisions that result in notable competitive advantages, propelling expansion and profitability within a highly competitive marketplace.
The crucial significance that manufacturing analytics play in contemporary industrial processes is reflected in the market’s projected significant rise worldwide. Estimated to be worth USD 5.5 billion in 2022, the industry is expected to rise at a remarkable 16.8% compound annual growth rate (CAGR) between 2023 and 2031. It is anticipated that the market would be valued USD 22.3 billion by the conclusion of this time. This quick expansion demonstrates how advanced analytics solutions are being used more widely in the manufacturing industry as a result of the demand for improved operational efficiency, real-time decision-making, and predictive maintenance. The manufacturing analytics market is expected to have a significant impact on how the global industry develops in the future as firms continue to invest in data-driven initiatives to maintain their competitiveness.
Manufacturing Analytics’ Development
Manufacturing analytics has had a revolutionary journey, mirroring the larger digital revolution in the industrial sector. In the beginning, production relied on human recording and simple computational tools for data collecting. Data collecting and analysis techniques evolved along with technology, thanks to the development of sensors, automated data gathering, and more complex software systems. We live in the big data age now, when enormous volumes of data can be analyzed instantly to produce insights that are useful. using unparalleled precision and speed, manufacturers can now foresee obstacles and grab opportunities using predictive and prescriptive analytics, which estimate future occurrences and prescribe actions. Descriptive analytics just reports what has happened
Important Elements of Industrial Analytics
A number of fundamental elements form the basis of manufacturing analytics, which combine to offer thorough insights into production processes. Data collection is the cornerstone, wherein information is obtained from a variety of sources, such as corporate systems, machines, and sensors. The next step is to incorporate this data into a coherent system so that analysis may be done easily. Processing in real-time is essential because it makes it possible to see problems or opportunities as soon as they appear. Intelligent algorithms and machine learning are examples of advanced analytics approaches that are essential for deciphering data, finding trends, and forecasting information that may guide choices. When combined, these elements provide a strong environment that facilitates industrial processes’ ongoing development.
How Operations Are Transformed by Manufacturing Analytics
The capacity of manufacturing analytics to offer in-depth understanding of every facet of production is what gives it its revolutionary potential. Manufacturers are able to increase efficiency, decrease waste, and limit downtime by employing data analysis to make better decisions, ranging from the shop floor to the supply chain. Analytics, for instance, may show inefficiencies in manufacturing lines, enabling businesses to reorganize procedures for maximum efficiency. Additionally, by highlighting patterns in machine performance, it can provide preventative maintenance before problems worsen and result in expensive failures. Furthermore, producers may guarantee that they reach or surpass production objectives, resulting in more constant output and improved customer satisfaction, by monitoring and evaluating key performance indicators (KPIs)
Using Analytics to Improve Product Quality
By giving real-time visibility into production processes and spotting any problems before they have an impact on the finished product, manufacturing analytics plays a critical role in improving the quality of products. Through the examination of data from several phases of production, producers are able to identify the underlying reasons for errors and take remedial measures to avoid them happening again. Analytics facilitates the constant meeting of quality requirements by optimizing production factors including temperature, pressure, and speed. This degree of control is especially crucial in sectors like the manufacture of medical devices, automobiles, and aircraft where accuracy and reliability are critical. Manufacturing analytics assists businesses in producing higher-quality goods that satisfy customers and legal requirements by lowering variability and guaranteeing specification conformance.
Cutting Down on Waste and Enhancing Sustainability
Sustainability is becoming more than just a catchphrase in today’s manufacturing world—it is a vital economic need. Manufacturing analytics is essential for assisting businesses in cutting waste and enhancing their sustainability initiatives. Analytics enables manufacturers to pinpoint areas where resources—materials, energy, or time—are being squandered and to put policies in place to maximize their usage by giving real-time monitoring of resource consumption. For example, analytics can identify energy usage inefficiencies and lead to changes that lower the total carbon impact. In a similar vein, businesses may cut waste and scrap production by monitoring the use of raw resources. These advancements support environmental sustainability as well as economic savings, which is in line with the increasing demand for eco-friendly production methods from customers and authorities.
Overcoming Obstacles in Manufacturing Analytics Implementation
Manufacturing analytics implementation is not without difficulties, despite its many advantages. The existence of data silos, where information is kept in separate systems that are not in communication with one another, is one of the main obstacles. Making data-driven choices and gaining a complete picture of operations may be hampered by this lack of integration. Furthermore, it can be extremely difficult to integrate analytics tools with current industrial processes, necessitating large infrastructure and technological expenditures. The requirement for knowledgeable staff to handle and comprehend the data produced by these technologies is another difficulty. The need for data scientists and analysts with knowledge of manufacturing processes is growing as production becomes more data-driven. A deliberate approach is needed to overcome these obstacles, one that involves upskilling the workforce, establishing a data-driven culture, and investing in technology that facilitates integration.
Manufacturing Analytics’s Future
Future manufacturing analytics holds even more advanced tools and methods that will help manufacturers remain competitive in a world that is becoming more and more data-driven as technology advances. It is anticipated that developments in machine learning and artificial intelligence will significantly expand analytics’ potential, allowing for better informed decision-making and more precise forecasting.
Even more insight into production processes will be possible with the combination of Internet of Things (IoT) and industrial analytics, enabling real-time modifications and more effective operations. Furthermore, analytics will become more scalable and accessible with the growing usage of cloud and edge computing, allowing businesses of all sizes to gain from data-driven insights. Manufacturing analytics will become increasingly more crucial as these technologies develop in terms of fostering innovation, enhancing productivity, and guaranteeing sustainability in the manufacturing sector.