By Chandrima Chatterjee
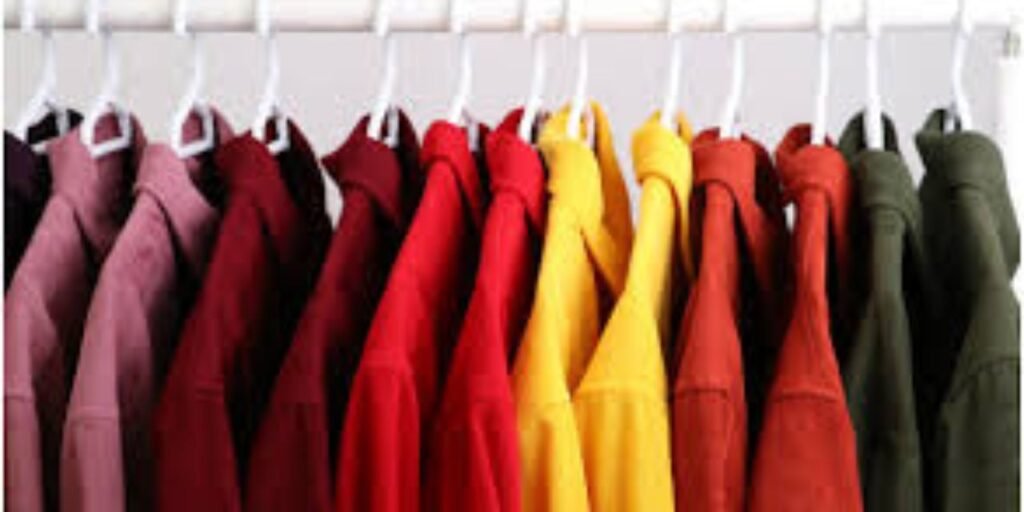
The EU is the second-largest export market for Indian T&A products, hence the sector is very eager to finalise the free trade agreement with them. (Source: Reuters)
There aren’t many investment incentives available for MSME businesses, which make up the majority of the sector, since the Technology Upgradation Fund Scheme (TUFS) was discontinued.
By 2030, India hopes to export $100 billion worth of textiles. In order to maximise the benefits of free trade agreements, Chandrima Chatterjee proposes addressing non-tariff barriers encountered by exporters and making adjustments to quality control orders for textile goods ahead of Budget 2025.
The state of the textile and clothing industry today
With exports rising 6.93% from April to November 2024 compared to the same period in 2023, the Indian textile and apparel (T&A) sector has done well in the current fiscal year. With an 11.3% increase in exports, the clothing industry is the main driver of this expansion. The increase is ascribed to the growing demand for Indian T&A goods in important markets such as the
the US and the EU. The sector has high hopes of maintaining this pace for the remainder of the fiscal year. As the sixth-largest exporter in the world in 2023, India is a major force in the global textile and apparel business. About 8% of India’s total exports in 2023–2024 came from this industry.
The industry’s expansion could be hampered by doubts about the continuation of some crucial programs, such as the Interest Equalisation Scheme and the Remission of Duties and Taxes on Exported Products (RoDTEP) for advance authorisation (AA), special economic zones (SEZ), and export-oriented units (EOU), past December 31, 2024.
Announced quality control orders for textile items
The government issues Quality Control Orders (QCOs) as regulatory directions to make sure that certain items fulfil required safety and quality criteria. QCOs are mandatory, meaning that makers, importers, and dealers must adhere to the established standards, in contrast to the optional Bureau of Indian Standards (BIS) rules.
The goal of adding QCOs to textiles for certain man-made (MMF) fibres, filaments, and yarns is to improve the quality of the final product. The execution strategy, however, is the main issue facing the sector. Around the world, these mandated quality standards are often implemented top-down, starting with final products.
In contrast, raw materials like fibres and yarns are the main emphasis of quality requirements in India.
Do QCOs provide any difficulties?
Due to the fact that many foreign suppliers have not yet obtained BIS certification, the current strategy has restricted the supply of several raw materials. These requirements only apply to physical exports, not intermediate suppliers, even if AA, SEZ, and EOU units are permitted to exclude imports. Manufacturers of some specialist downstream goods have suffered as they are reliant on imports of these raw materials since they are not readily available locally in the necessary quantity and quality. The next commodity in the value chain, such fabric and clothing, may be imported in large quantities as a result, which would hurt domestic producers’ interests.
As a result, the policy pertaining to QCOs urgently needs to be reviewed, and before introducing any new QCOs, an impact assessment must be completed. QCOs might begin with the clothing in order to achieve the goal of having high-quality final products.
Fibre costs and investment strategies
The cost of Indian fibre, such as cotton and MMF, is between 12% and 30% more than that of rivals. The cost-competitiveness of the clothing and makeup is eroded as a result of it, which ripples down the value chain. The government must eliminate import taxes on all types of cotton and liberalise the import regulations for MMF fibres in order to guarantee the supply of raw materials at costs that are competitive with those of other countries.
There aren’t many investment incentives available for MSME businesses, which make up the majority of the sector, since the Technology Upgradation Fund Scheme (TUFS) was discontinued. MSMEs need programs similar to TUFS, which offer upfront capital subsidies and streamlined processes to guarantee capacity creation, especially in downstream areas, in order to draw in additional investments.
Making use of free trade agreements
Free Trade Agreements (FTAs) provide the textile and clothing industry more market access, tariff rebates, and a fair playing field against international rivals. India has struck a contract with the European Free Trade Association (EFTA) and trade agreements with key T&A markets, including the United Arab Emirates, Australia, and Mauritius. Finalising the free trade agreement with the EU, the second-largest export market for Indian T&A goods, is of special interest to the sector.
The government may also negotiate on the several non-tariff/technical hurdles that Indian exporters may encounter while exporting to these nations in order to optimise the advantages of free trade agreements. For example, while the UK and the EU are developing strict quality standards, the Indian government, through the BIS, is also developing standards that are comparable to those of other countries. Bilateral trade can be further stimulated by negotiations for mutual recognition of testing and quality standards.
The writer is secretary-general of the Confederation of Indian Textile Industry.