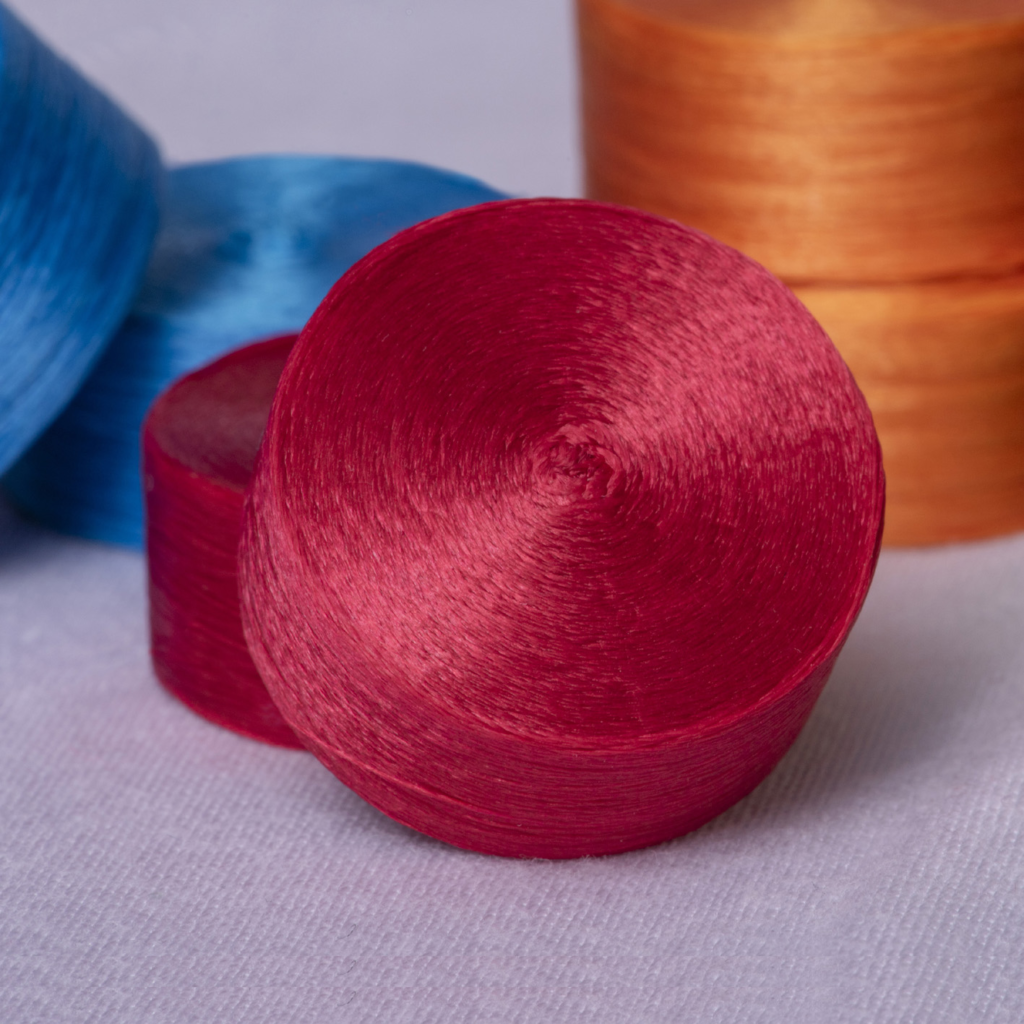
Durak Tekstil, Turkey’s leading developer of industrial sewing and embroidery threads, is currently making plans for a new and expanded factory at its base in Bursa, as well as opening a regional office in North America next year.
A continuous focus on R&D and the launch of some very highly-differentiated products is driving the success of this third-generation family-owned company which was initially founded in 1971 to provide Turkey with fishing net twine – at that time 100% imported.
Durak then expanded into the production of rayon and polyester embroidery threads before successfully diversifying into a wide range of niche and specialised markets, while growing an international customer base. This growth has been accompanied by continuous investment in the latest advanced production technologies.
“We now manufacture around 350 separate products and our portfolio is constantly being updated,” says Yigit Durak, third generation member of the company’s board, who brims with enthusiasm when detailing his company’s developments. “It’s our focus on research and development which I believe really sets us apart as a company. Deep know-how of the technical possibilities of our machines and processes is enabling us to continue to bring new products with advanced functionalities to the market.”
Centreless Duma
Among winning products is Duma®, a centreless pre-wound under-bobbin made from strong continuous polyester filaments which is available in various sizes and thanks to careful selection of raw materials and the use of unique lubrication methods retains its exact tension from beginning to end.
“The precise winding method with Duma keeps the variation in length to under one degree, so that a bank of bobbins can be changed at precisely the same which enables very concrete savings to be made,” Durak explains. “Because of the lack of centre and the compaction of the yarn, we get three times the amount of product on each bobbin and the result is a high reduction in the times required for changes. We have calculated that over the course of a shift, this is achieving what could normally be produced on twelve advanced machines with just ten.”
Working on a similar principle is the Duraless® hollow core thread, and both have a melting points of 260ºC and soften at between 220-240ºC. A very high heat tolerance is achieved compared to conventional sewing threads when the shrinkage rate at 150ºC is calculated to be less than 1%. The threads show high resistance to most mineral acids, are unaffected by bleaching and micro-organisms and do not deteriorate in washing and dry cleaning.
Functionality
Other innovations focus on functionality, including the new SilverPro conductive thread for smart textiles and wearable technologies, luminous Milky Way, Redolent scented thread, the Fire-Safe range of meta-aramids and para-aramids and the Cut Safe range manufactured from various combinations of UHMWPE, glass fibre and elastane.
“Despite many obstacles in 2023, we managed to grow the business and this year anticipate further growth of around 30% and now export to over 100 countries,” says Yigit Durak in conclusion. “Research and development remains the bedrock of our business and our entire 300-strong team in Bursa holds regular brain-storming sessions to fully explore new concepts and ideas. The success stories are fully certified and patented prior to launch and today approximately 20-25% of our total turnover is provided by technical threads. This will only increase in the future.”