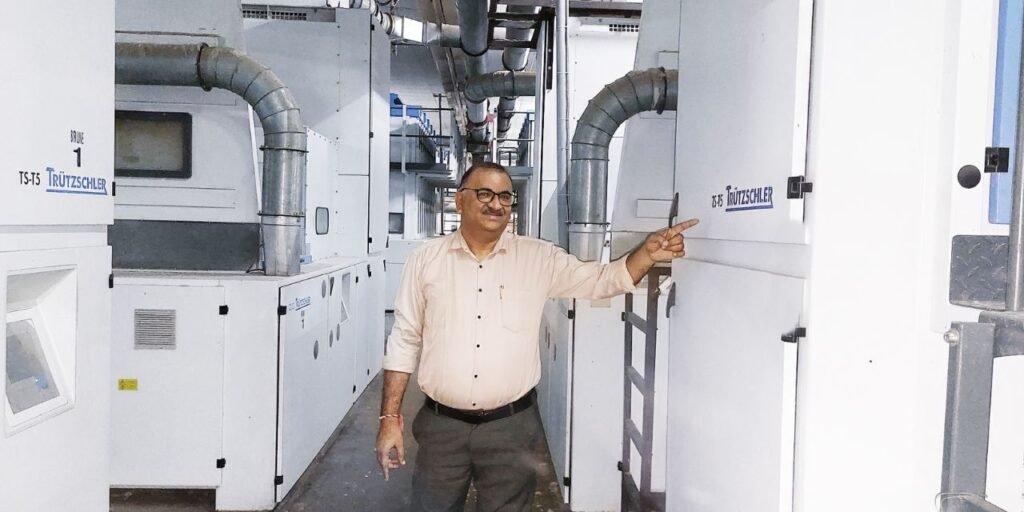
February 12, 2025 – Mönchengladbach
Removing foreign contaminants from cotton is a critical challenge in the textile industry. To tackle this, Trützschler’s T-SCAN technology integrates multiple detection modules that identify and eliminate impurities during the blowroom process. Initially introduced in cotton ring spinning, T-SCAN is now proving its effectiveness in rotor applications, benefiting Indian textile manufacturers.
When raw cotton reaches spinning mills, it often carries unwanted materials like leaves, plastic, jute fibers, or metallic particles. While standard cleaning processes remove most impurities, some foreign elements especially polypropylene and colored contaminants—remain a major concern. These materials can cause yarn breakage, uneven dye absorption, and fabric defects, leading to product rejections.
To combat this issue, Trützschler’s TS-T3 and TS-T5 foreign part separators offer an advanced solution. These systems efficiently detect and remove low-contrast, small, or thread-like contaminants, including transparent and glossy polypropylene fibers. This makes them particularly valuable for the rotor and recycling segments, where contamination control is crucial.
Proven Performance in the Indian Market
Several leading Indian manufacturers have successfully implemented TS-T3 and TS-T5 technologies:
✅ Nandam Terry & Nandam Denim (Ahmedabad): Producing 45 tons of denim and 10 tons of terry towel fabric daily, they report a significant reduction in color contamination and improved fabric quality. “Our contamination-controlled yarn is now preferred by high-end brands,” says Ashish Raval, Vice President, Spinning.
✅ Thiagarajar Mills Ltd. (Madurai): Operating 25 Trützschler machines for denim yarn production, the company confirms superior contamination removal in rotor spinning. “TS-T5 enhances yarn quality and simplifies maintenance,” states Muthupalaniappa M, Senior Vice President (Technical).
✅ Blue Rose Cotspin LLP (Northern India): Producing 20 tons of yarn per day, primarily for hosiery and weaving, the company has seen a remarkable improvement in yarn purity since installing the TS-T3. “We no longer receive contamination complaints,” says Ashwani Garg, Managing Director.
✅ Patiala Gold LLP (Punjab): Specializing in rotor yarn production for bottomwear and bedsheets, this manufacturer praises the TS-T3’s efficiency and ease of maintenance, which significantly reduces downtime. “Our production efficiency has increased compared to other foreign part separators,” notes Kamal Kumar, Owner.
Minimal Maintenance, Maximum Efficiency
The TS-T3 and TS-T5 models ensure highly effective contamination removal with minimal fiber loss. These energy-efficient systems consume up to 80% less compressed air than conventional solutions, reducing operational costs. Additionally, their automated calibration and user-friendly design make maintenance effortless for textile mills.