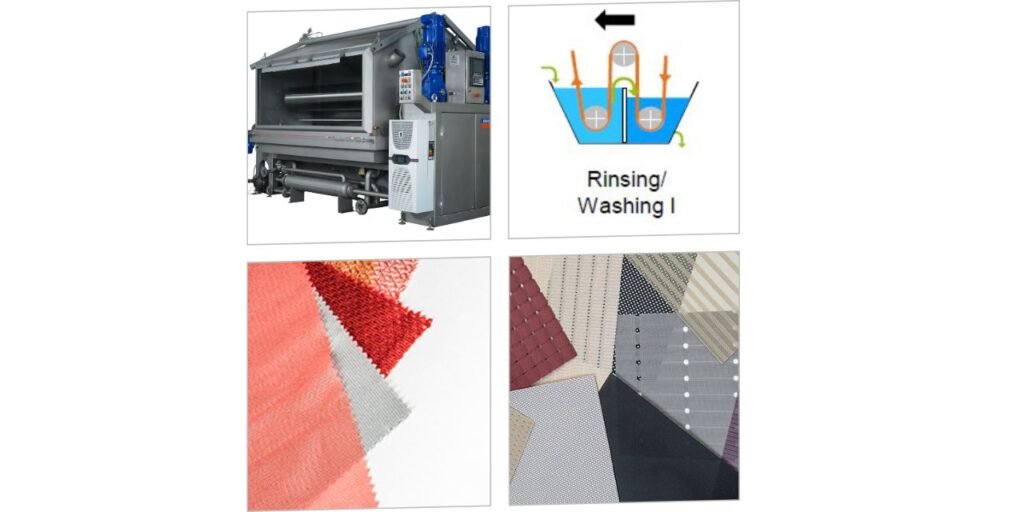
For picky dyers, Benninger’s advanced jigger is the ideal option.
Switzerland, Uzwil, October 29, 2024 Benninger, a world authority in the creation and manufacturing of textile finishing systems, created a jigger that performs very well in the field of discontinuous fabric dying, perfect for complex and delicate textiles. Benninger JigMaster has cutting-edge technologies that enable dyers to enhance their operations while lessening their negative effects on the environment. Consumers are thrilled; Swisstulle is a prime example.
JigMaster demonstrates state-of-the-art technology that satisfies the requirements of contemporary textile production. The system, created in Switzerland and manufactured at Benninger’s cutting-edge plant in Pune, India, is a major development in fabric dying equipment and is ideal for businesses such Swisstulle needs equipment to meet the strictest requirements for sustainability, quality, and accuracy.
An ideal match for Swisstulle’s exacting requirements
JigMaster was chosen by Swisstulle http://(www.swisstulle.ch),, a market leader in Europe for technical knitted materials and traditional bobbinet tulle, to enhance its textile dyeing and finishing procedures. This strategic decision was made with the intention of significantly improving the company’s manufacturing capabilities, namely in the areas of high-quality technical textile washing and dyeing. With more than a century of expertise, Swisstulle is still at the forefront of innovation, guaranteeing the best quality and sustainability in its products.
Swisstulle provides its well-known bobbinet tulle and technical textiles to a variety of industry sectors, including the fashion and automotive sectors. JigMaster is essential to achieving their production targets in the field of technical textiles for high-demand uses like sun protection.
According to Achim Brugger, CEO of Swisstulle, “Benninger JigMaster offers Swisstulle a new level of efficiency and sustainability, perfectly aligned with our commitment to resource-conscious production.” By incorporating the JigMaster into its manufacturing process, Swisstulle guarantees that their textiles won’t not only fulfil but also surpass client expectations while promoting its environmental responsibility.
Because of its plug-and-play nature, the machine can be quickly set up and seamlessly integrated into current production workflows, reducing downtime and increasing productivity.
Transforming the dyeing of textiles
Benninger JigMaster’s TwinJig technology, which has two separate troughs and allows Swisstulle to save up to 35% on water usage during washing, is one of its best features. Additionally, this technique maximises energy use, improving the eco-friendliness of the dyeing process without sacrificing the quality of the cloth. By using less water and steam, the machine’s excellent mechanical washing effect and counterflow rinsing further improve resource savings. Considering the textile industry’s increasing emphasis on sustainability, these are noteworthy benefits.
Additionally, JigMaster provides quick heating gradients that speed up production while preserving excellent fabric care thanks to two high-capacity heat exchangers. The exact speed and tension control provided by its BEN-CONTROL software is crucial for Swisstulle’s exquisite textiles, which call for low- tension colouring to prevent edge lines or wrinkles. The machine also has accurate length measurement and sample point detection capabilities, which guarantee constant quality throughout the manufacturing process.
A collaboration that is future-proof
The collaboration between Swisstulle and Benninger demonstrates the firms’ mutual dedication to sustainability and innovation.After JigMaster is installed, we fortify our standing as a progressive textile producer. In order to create high-performance textiles effectively and sustainably, we employ the most advanced equipment,” Brugger explains.