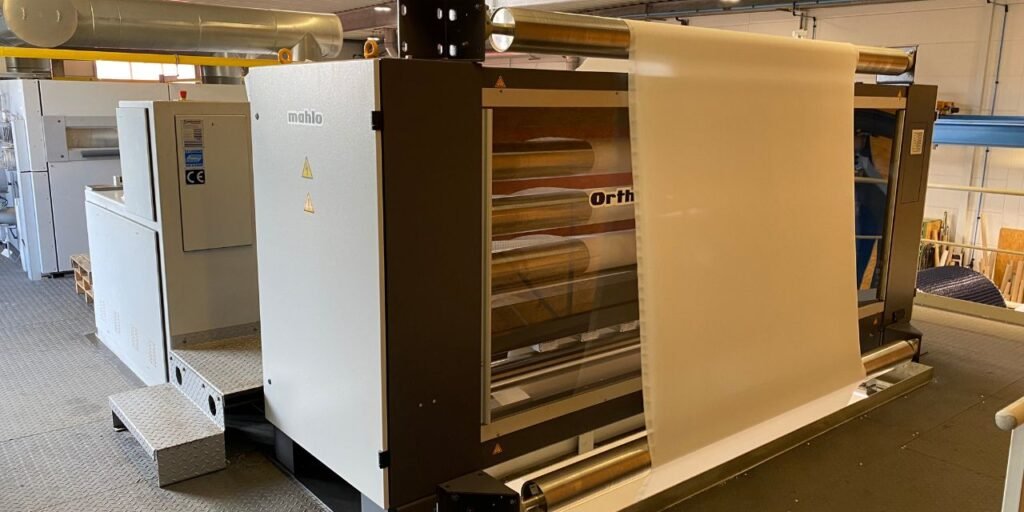
Using cutting-edge measurement and control technologies from Mahlo, SAATI Germany, a top producer of extremely advanced technical textiles, has further improved its manufacturing processes. This year, the business advanced from installing its initial Mahlo systems in 2020.
Among other things, the internationally active SAATI Group manufactures functional fabric for smartphones and tablets, aramid fabric for protective vests, and filter fabric for blood transfusion equipment. SAATI is renowned for its exceptional quality and precision, which are upheld throughout the whole production process. Since many of the materials produced must serve essential purposes, such as in the security or medical technology industries, the high quality standards are very crucial.
As part of this optimisation process, a Famacont PMC-15 yarn density meter and a Mahlo distortion control system Orthopac FMC-15 were installed in the stenter frame’s outfeed.
The precise thread count (up to more than 300 F/cm) is a crucial quality element since Saati manufactures extremely technical textiles. This parameter may be continually recorded and logged using the PMC-15, a camera-based measurement device. By automatically regulating the stenter frame’s take-off roller, the FMC 15 simultaneously captures any remaining distortion and helps to remove what is known as “back sheet distortion” from the fabric. This minimises possible sources of mistake and guarantees consistently high-quality final goods.
SAATI started the next phase of process optimisation in 2024 since the investment in these systems was so successful. “We have further improved the control of fabric quality by installing an Orthopac GRVMC-15 straightening machine prior to the stenter frame’s infeed,” explains Thomas Brockmeier, operations manager. With a working width of 2,800 mm, the heavyweight Mahlo straightening system allows SAATI to rectify bow and skew distortions in the raw fabric before to the stenter frame. This is because even a small amount of skew or curvature in the weft thread can make the cloth useless or unappealing.
SAATI now has a completely automated system with the most monitoring and control possibilities possible thanks to the combination of the GRVMC-15 and the FMC-15 that was previously placed in the outfeed. The organisation is able to supply exactly shot-straight things because these two technologies work together. Brockmeier comments, “I am thrilled that we were able to finish the project so successfully.” “This means an improvement for us in terms of production reliability and quality.”
In addition to enhancing SAATI Germany’s manufacturing capabilities, the effective integration of Mahlo technology highlights the company’s exacting standards for product quality and accuracy. As a result, SAATI is achieving a significant competitive edge in the worldwide market and continuing to set an example of efficiency and innovation in the textile sector.