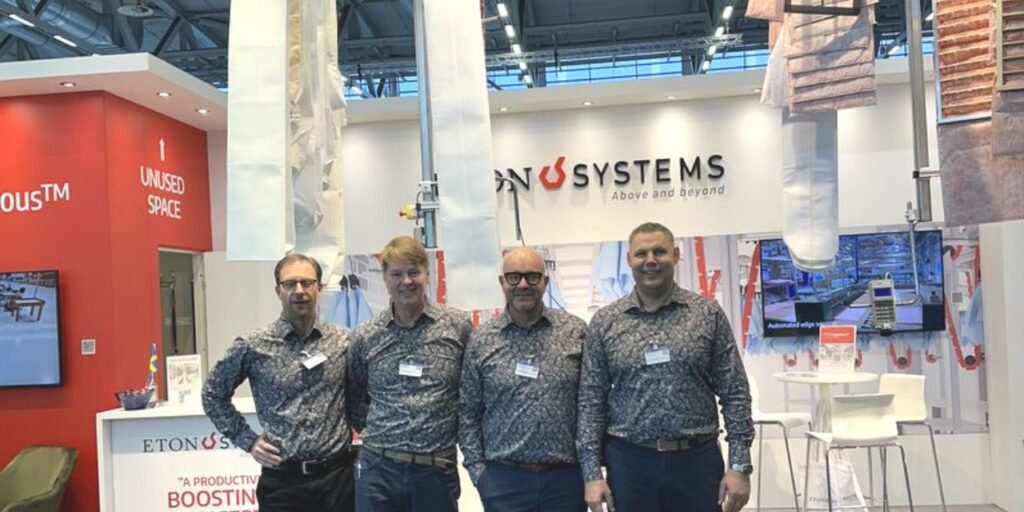
The filtration business, a sometimes unseen but vital component of the worldwide textile industry, depends on the manufacturing and automation services provided by members of TMAS, the Swedish Textile Machinery Association.
In practically every aspect of 21st-century living, technical woven and nonwoven textiles are utilised in a vast array of goods in filtration systems for air, gas, and liquid filtration.
They are used in air conditioning systems, domestic appliances like washing machines, and a wide variety of industrial activities in addition to being essential to road and aircraft traffic. vacuums.
For instance, Interfil produces 230,000 air filter units annually at its Skjåk production facility in Norway, using an astounding array of about 15,000 variations, with 9,000 items continually passing through the various plant stages at any given time. time every day, and 1,100 goods are produced each day.
The scenario is comparable at Filtration System Products’ (FSP) US facility in Farmington, St. Louis, which now produces more than 2,200 filter hoses and media per day.
Material handling
TMAS member Eton Systems’ automated material handling skills are essential to both Interfil and FSP.
Eton’s individually addressable product carriers are made to reduce handling and do away with human transportation around a production facility, guaranteeing that every single product gets to its designated location exactly when it’s needed for every distinct stage of the procedure.
Since a 50-meter overhead conveyor system was created and put in place to connect the company’s two production rooms at the Skjåk factory in 2014, Interfil has depended on Eton automation to do away with the need for truck transportation and manual handling. between the establishments. Due to the requirement for fewer vehicles, this has improved on-site safety while simultaneously resolving the issue of semi-finished items being produced distant from the final assembly area. It has also improved efficiency, quality control, and component traceability across the whole manufacturing process.
Using the same number of workers and the same working hours as the prior manual system, FSP has projected that after adopting an Eton system in 2023, its manufacturing output has grown by 60%. The inherent character of Eton A far more effective quality control procedure is made possible by the system’s guarantee that only flawless items are unloaded from it. Furthermore, Eton’s efficient technique of transferring individual units through the manufacturing process has reduced floor space and improved worker safety and ergonomics.
Because there are so many stylistic variants, FSP wasn’t sure if an automated manufacturing system could meet the needs of producing filtering media. However, our solution allows all carriers to be tracked in real-time and showed to be the ideal remedy’, Jerker Krabbe, CEO of Eton, adds.
Production of filter bags
Meanwhile, TMAS members ACG Kinna Automatic and ACG have created a completely automated microfactory for the manufacturing of entirely completed filter bags. Nyström and Juki Central Europe, in collaboration. Up until recently, third-party vendors have built and completed woven or nonwoven needlefelt filter bags using time-consuming and difficult cut and sew processes.
“Many hours of labour-intensive manual work that were previously required are no longer required due to the automation of these crucial steps,” explains Christian Moore, CEO of ACG Kinna Automatic. 120 completed filter bags are produced every hour, and The most recent high-definition vision cameras manage quality control, while accurate automated steering and alignment guide the complete setup. Not just for filter bags, but for many other businesses that depend significantly on these consumables for their operations, this kind of automation is the way to go.
The Smart Filter Line (SFL) and the Filtermaster 2.0 are two distinct interconnected modules that form the foundation of the ACG microfactory’s architecture. The SFL is in charge of feeding the fabric from rolls and folding it before sewing.
construction, which, depending on the requirements, may involve welding, mechanised stitching, or sewing and taping. Modular seaming techniques may be switched over very quickly when a product is changed. Following precision cutting to size for each unit, the now entirely tubular cloth is further folded in preparation for feeding it into the Filtermaster 2.0.
Using a second Juki sewing head on a robotic arm, the Filtermaster 2.0 then automatically fastens the bottom, snap rings, and reinforcement to the filter tube to create the completed filter bag that is prepared for shipment.
According to TMAS, “Our companies’ innovations are diverse and distinguished by a sophisticated understanding of automation techniques and the need for more sustainable processing methods that are being demanded by their customers.” Therese Premler-Andersson, Secretary General. “Textile manufacturers, particularly those in Europe and the US, are finding that reducing handling and doing away with manual transportation is crucial to giving them a competitive edge.”