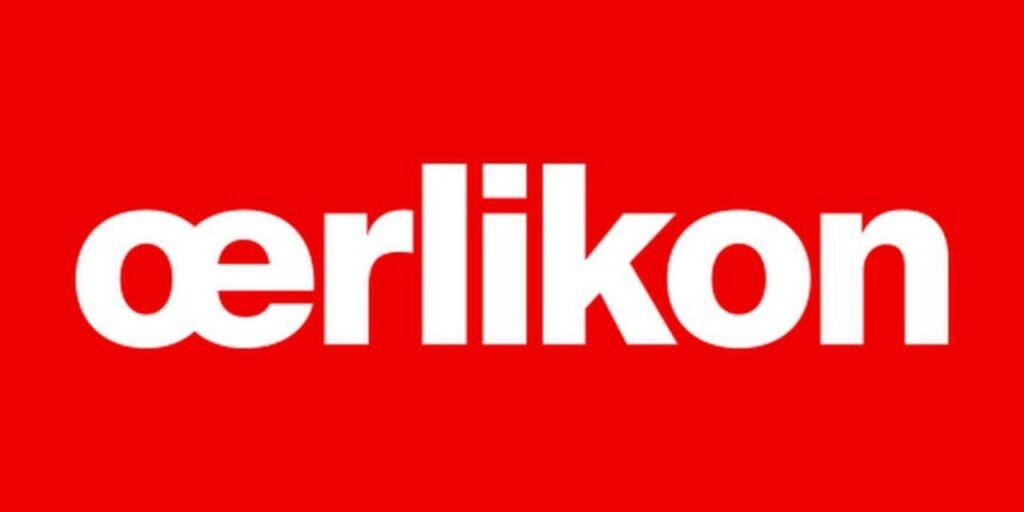
Berlin, September 02, 2024 – Oerlikon Nonwoven will showcase its customer- and market-driven system solutions for filtering applications at FILTECH, the premier trade show for filters and filtration systems in Cologne from November 12–14. The plant engineering business for nonwoven production technology, located in Neumünster, is inviting trade show attendees to meet the team at hall 8, exhibit B18, and see the company’s extensive product and process knowledge firsthand.
Filtration: Top meltblown solutions to meet the most demanding requirements Oerlikon Nonwoven meltblown technology makes it possible to produce distinctive and extremely complex nonwovens for sorption, insulation, and filtering applications in an effective and straightforward manner. The range of applications for filter media and membranes is matched by the diversity of polymers utilized in their manufacture. The spectrum includes specialty plastics like PPS and TPU as well as traditional polyolefins like PP and PE, PET, PLA, PBT, and PA. The Oerlikon Nonwoven Meltblown technique may be used to securely process all of these raw materials as well as others.
A conventional FFP2 filter medium’s pressure loss may be lowered to less than a quarter by using the extremely effective electret filter media produced by the hycuTEC hydrocharging technology, which has won the Edana Filtrex Innovation Award. According to Dr. Ingo Mählmann, Director of Sales & Marketing at Oerlikon Nonwoven, “Filtration efficiencies of over 99.99% are easy to achieve with typical filter media of around 35 g/m² with a maximum pressure loss of 35 Pa.” “What’s more, this innovative process eliminates the need for an additional drying process for the production of high-separation electret filter media for most applications,” he continues.
High-performance technology for filter applications: spunbond solutions
In filtration applications, spunbond products are playing a bigger role as the filter media itself as well as the supporting materials for the media. Customer-specific needs for various functions can be realized because of a nonwoven structure designed for their particular activities; it is also conceivable to integrate many functionalities into a single layer. Years of expertise in the field of bicomponent spinning techniques, in particular, have made it possible to build entirely new nonwoven structures and, as a result, fulfill several purposes with a single material. Different fiber cross-sections may be coupled using the Oerlikon Nonwoven Bico spunbond method, which also allows for the simultaneous production of several fibers from one or more polymers on a single system. The spectrum includes splitable fibers and so-called mixed fibers in addition to the traditional core-sheath and side-by-side bico filaments.